Actt Service Program Sp 3-872-009 Shut Down Harness & More
Introduction Actt Service Program Sp 3-872-009 Shut Down Harness
The SP 3-872-009 Shut Down Harness, a crucial part intended to improve safety in industrial environments, was introduced by the ACTT Service Program. This creative harness is crucial to ensuring the safe and timely shutdown of machinery and operations during crises. Its application is an essential safety precaution against unanticipated circumstances that might endanger employees and valuable equipment, not merely a matter of compliance.
Having dependable safety measures is crucial in industrial settings because there is a significant chance of unforeseen occurrences. When faced with urgent conditions, the SP 3-872-009 Shut Down Harness allows for quick action, which eases anxiety. Its design successfully reduces the chance of catastrophic incidents by demonstrating the dedication to putting safety first.
This harness is an excellent example of safety procedure best practices in addition to meeting regulatory requirements. Organizations may safeguard their employees and maintain operational integrity by including such cutting-edge safety measures, which makes the SP 3-872-009 a vital tool for any industrial enterprise dedicated to upholding a safe working environment.
ACTT Service Program SP 3-872-009: What is it?
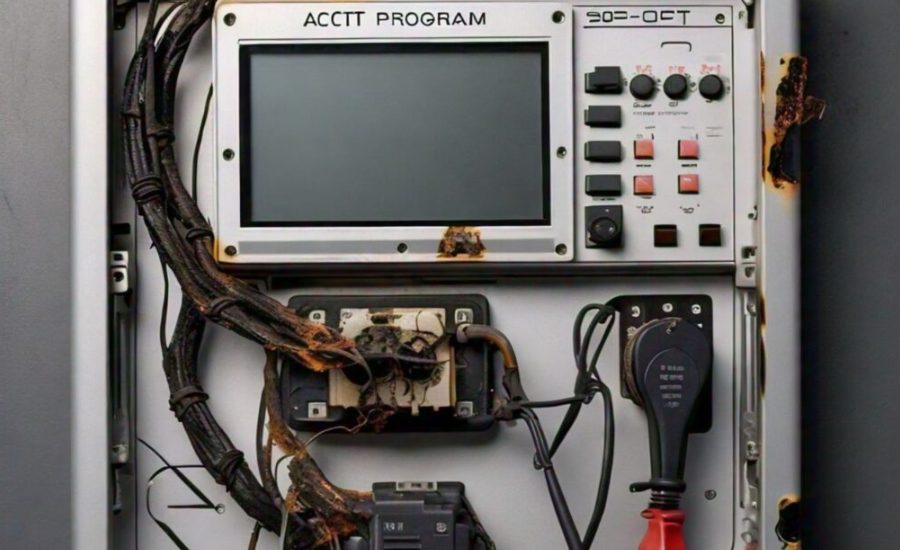
The ACTT Service Program has evolved the SP three-872-009 Shut Down Harness, a cutting-edge answer designed to beautify protection in commercial operations. This harness is expertly crafted to allow rapid shutdown of machinery at some point of emergency conditions, efficiently prioritizing the well-being of operators whilst safeguarding gadget from capability harm.
When irregularities rise up—which includes mechanical disasters or risky conditions—the harness activates an electricity cut-off mechanism. This set off movement is important for reducing dangers and avoiding mishaps that may endanger people and motivate luxurious equipment damage. The significance of proactive protection measures in tough work situations is validated through the SP 3-872-009.
By enforcing this superior harness, industries now not simplest follow protection rules but also demonstrate a dedication to retaining a stable operational surroundings. The thoughtful design of the SP 3-872-009 reinforces the significance of dependable protection protocols, permitting organizations to unexpectedly cope with emergencies and maintain their operational integrity. As safety is still a pinnacle priority in commercial settings, the SP 3-872-009 Shut Down Harness sticks out as a vital device in selling a tradition of safety and responsibility.
Importance of the ACTT Service Program SP 3-872-009 Shut Down Harness
The shutdown harness plays a vital role in the overall power management of an aircraft, functioning as a key control point for electrical distribution. This intricate part makes certain that electricity is efficiently distributed throughout the aircraft’s many systems, giving each the energy it needs without ever reaching an overload.
The harness’s capacity to serve as a safety measure in an emergency is one of its primary uses. It can quickly isolate electrical systems in emergency scenarios, greatly lowering the possibility of fire or other hazardous events that could compromise safety.
Additionally, the shutdown harness supports proactive maintenance through its diagnostic capabilities.Through ongoing performance monitoring, personnel may detect and resolve possible problems before they become more significant, thereby improving the aircraft’s overall reliability.
In summary, the shutdown harness plays a crucial role in maintaining both operational effectiveness and aviation safety. It is not merely an ordinary component.Its combination of power regulation, emergency response, and diagnostic support underscores its importance in maintaining the highest standards of safety and performance in modern aircraft.
Key Features:
- Emergency Response: The harness allows for immediate isolation of electrical systems, significantly reducing fire hazards and other safety risks in high-risk environments such as chemical processing and oil and gas industries.
- Durability: It is built to withstand extreme conditions, including high temperatures and corrosive substances, ensuring reliable performance in demanding settings.
- Regulatory Compliance: The SP 3-872-009 meets safety regulations and exemplifies best practices in safety protocols, reinforcing a culture of responsibility within industrial operations.
- Proactive Maintenance: Equipped with diagnostic capabilities, it facilitates ongoing performance monitoring, allowing personnel to identify and address potential issues before they escalate.
- Applications in the Energy Sector: The harness is specifically designed for high-pressure environments like power plants and oil refineries, ensuring safe operations under challenging conditions.
Overall, the SP 3-872-009 Shut Down Harness is essential for maintaining operational integrity and promoting a safe working environment in industrial applications.
Enhanced Operational Safety and Risk Management
The SP 3-872-009 Shut Down Harness plays a crucial function in raising operational safety requirements and coping with dangers in commercial environments. Its design prioritizes rapid reaction to emergency situations, enabling immediate shutdowns to prevent injuries or further device harm. By presenting a mechanism which can immediately disconnect strength for the duration of malfunctions, the harness minimizes downtime while additionally decreasing the ability for extreme incidents that could jeopardize both personnel and capital belongings. This proactive method to safety guarantees that industries can operate with self assurance, understanding that any dangerous scenario can be swiftly contained.
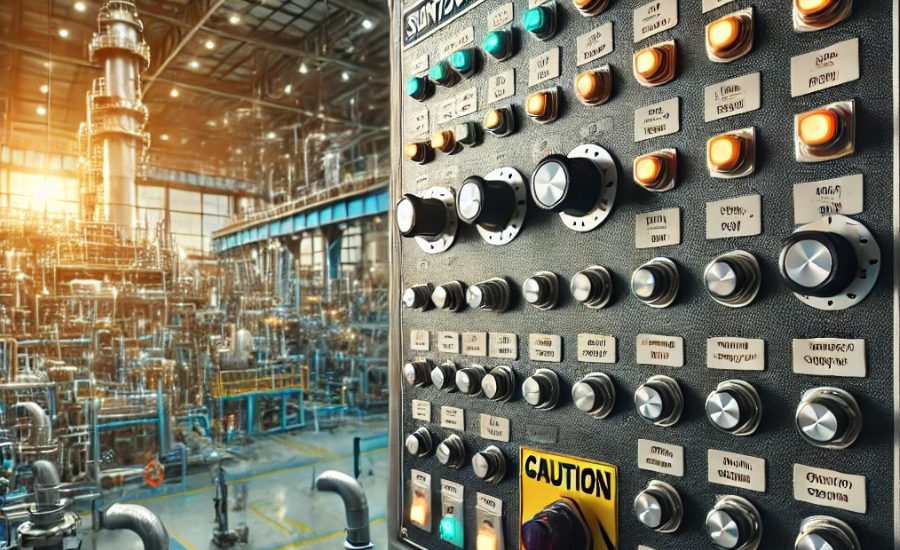
The harness is going past conventional safety measures through integrating advanced diagnostic skills, which enable ongoing tracking of system overall performance. This characteristic is vital in excessive-threat industries in which equipment operates below demanding conditions, because it lets in for early detection of issues which include electrical faults, mechanical wear, or machine overloads. Early intervention facilitated with the aid of the diagnostic functions not best extends gadget lifespan but additionally enables avoid steeply-priced maintenance and unplanned outages.
How Does the SP 3-872-009 Shut Down Harness Work?
The SP 3-872-009 shutdown harness is designed to integrate seamlessly with a machine’s power system. Its primary function is to ensure rapid power disconnection in emergency scenarios, triggered by either an emergency stop button or a detected fault within the equipment. This swift response is crucial for preventing further damage to machinery and protecting the safety of operators.
For example, hitting the emergency stop button triggers the harness and instantly shuts down the machine in the event of a malfunction or dangerous circumstance. The hazards of equipment failure, such as overheating, electrical malfunctions, or mechanical failures, are greatly decreased by this vital safety element.
The harness’s quick activation not only safeguards the machinery but also prioritizes the well-being of personnel working in potentially dangerous environments. By effectively managing power during emergencies, the SP 3-872-009 shutdown harness demonstrates its vital role in enhancing operational safety. This innovative solution underscores the importance of incorporating advanced safety measures into industrial equipment, fostering a secure work environment that minimizes risks and promotes a culture of safety.
Importance in Industrial Applications
The significance of the shutdown harness lies in its capacity to swiftly and efficiently stop operations without the need for human intervention. This automatic response is crucial in high-risk industries like chemical processing, oil and gas, and manufacturing, where the consequences of operational failures can be severe.
In these industries, the risks of using machinery when there is a malfunction can seriously endanger valued assets and employees. These sectors are able to maintain strict safety regulations by depending on sophisticated shutdown mechanisms, which guarantee that any anomalies result in an instantaneous stop to operations.
This preemptive strategy helps avoid expensive damage to facilities and equipment in addition to protecting workers. The harness’s emergency resilience improves operational integrity and fosters a safety culture in a variety of industrial settings.
Overall, the implementation of such automated safety measures is essential for managing risks effectively and protecting both human lives and capital investments. By prioritizing these systems, industries can ensure a safer working environment while maintaining compliance with regulatory requirements, ultimately contributing to more sustainable and secure operations.
SP 3-872-009 Shut Down Harness Design and Functionality
The thorough design of the SP 3-872-009 harness places a high priority on dependability and easy integration in industrial settings. Constructed to endure the most severe circumstances, it has a robust design that can tolerate high temperatures, high vibrations, and exposure to corrosive substances. High-quality materials are used to provide long-term performance in a variety of applications in addition to durability.
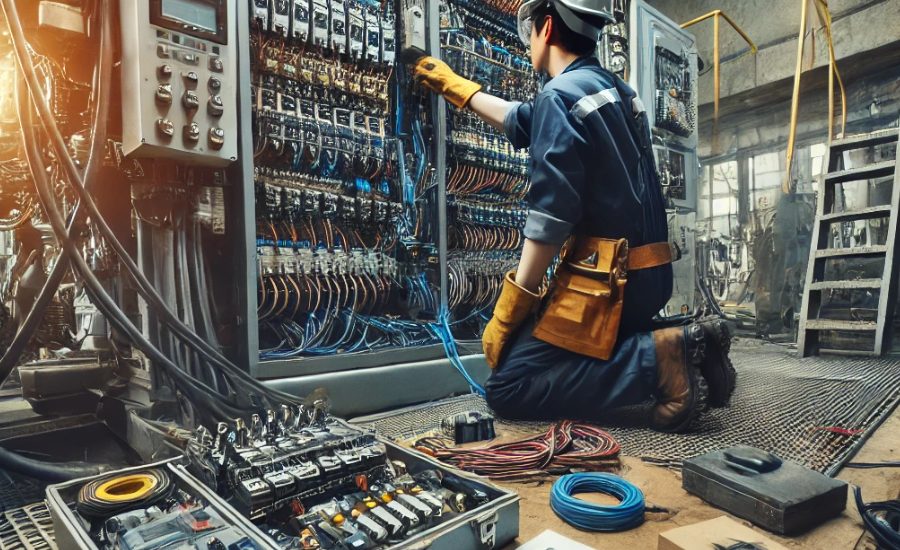
Functionally, this shutdown harness serves as a vital element within larger control systems. It connects to emergency stop buttons and similar devices, which operators can activate manually or automatically when hazardous conditions arise. Upon activation, the harness promptly sends a signal to halt operations, triggering a series of pre-programmed responses that safely bring machinery and processes to a controlled stop.
This proactive safety feature is crucial for averting mishaps and safeguarding both people and property. Industries can strengthen their safety standards and guarantee prompt and efficient handling of emergency situations by incorporating the SP 3-872-009 into their operational protocols. Overall, this harness is an essential part of any industrial setting because it not only maintains operational integrity but also strengthens the workplace safety culture.
Energy Sector
In the energy sector, where machinery functions under intense pressure and often hazardous conditions, the necessity for a dependable shutdown mechanism cannot be overstated. The ACTT Service Program SP 3-872-009 Shut Down Harness is specifically designed to manage equipment in environments such as power plants, oil refineries, and other energy production facilities.
This advanced harness plays a critical role in maintaining safe operations by providing a reliable means of controlling machinery. The SP 3-872-009 harness helps reduce the hazards related to equipment breakdowns or hazardous circumstances by guaranteeing prompt power separation in emergency scenarios. Its sturdy construction prioritizes safety over operational integrity and is made to endure the harsh conditions frequently encountered in the energy sector.
Utilizing the SP 3-872-009 harness not only adheres to safety regulations but also fosters a culture of responsibility within energy production facilities. By incorporating such a reliable shutdown system, organizations can enhance their overall safety protocols, safeguarding both personnel and assets while ensuring uninterrupted operations. Ultimately, this harness represents a vital investment in the safety and efficiency of energy operations, helping to navigate the challenges of a high-stakes industry.
Overheating Components
If a piece of machinery’s overheating is not quickly fixed, it may cause major operational problems. Proactive action is necessary to manage this risk effectively:
Check Wiring: Start by carefully inspecting each connection for evidence of fraying, corrosion, or deterioration of the insulation. Overheating and electrical system integrity can be caused by defective wiring.
Assess Load Distribution: It is crucial to monitor the distribution of electrical loads across components. Check that no single part of the system is drawing more power than it is designed to handle, as this imbalance can contribute to overheating and potential breakdowns.
You may drastically lower the chance of overheating and the risks that go along with it by putting these preventive steps into practice. In addition to extending the life and performance of equipment, preventive maintenance and careful observation also help to create a safer workplace. By taking these precautions, you can make sure that systems run well and lower the likelihood of unforeseen problems, which will eventually protect both people and important assets. Maintaining operational reliability in any industrial setting requires putting electrical safety and load control first.
Future-Proofing Industrial Safety Practices
As industries hold to include automation and clever technology, the SP 3-872-009 harness is properly-positioned to guide destiny-proof protection techniques. The harness’s capacity to interface with advanced tracking systems and IoT (Internet of Things) gadgets manner it may be seamlessly included into modern-day business manage networks. This integration permits real-time data collection and faraway monitoring, providing insights which could inform predictive maintenance schedules and optimize safety protocols.
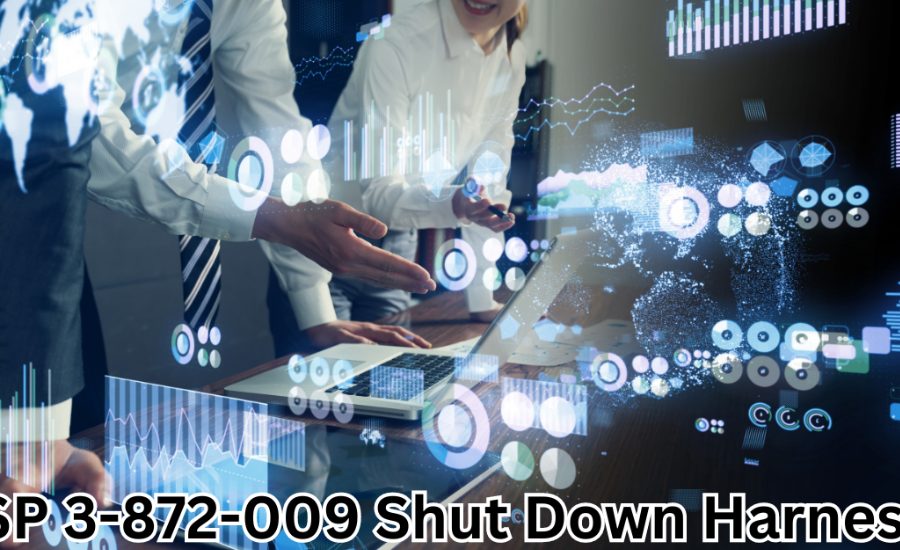
The adaptability of the SP 3-872-009 additionally guarantees that it can evolve along technological improvements in machinery and safety system. As industries adopt new standards for machine safety, the harness can be upgraded or customized to fulfill emerging necessities, making it a sustainable investment for corporations dedicated to lengthy-time period safety development. By incorporating the SP 3-872-009 into their protection infrastructure, agencies no longer best comply with cutting-edge safety standards but additionally role themselves at the vanguard of destiny safety improvements.
FACT:
- Purpose: The SP 3-872-009 Shut Down Harness enhances safety in industrial settings by providing a reliable mechanism for the rapid shutdown of equipment during emergencies.
- Functionality: The harness is activated by emergency stop buttons or fault detection in machinery, ensuring immediate power disconnection to prevent further damage and protect operators.
- Industrial Applications: It is particularly crucial in high-risk industries such as chemical processing, oil and gas, and manufacturing, where operational failures can pose severe risks to safety and equipment integrity.
- Design: The harness is built to withstand extreme conditions, including high temperatures, vibrations, and exposure to corrosive substances, ensuring long-lasting performance and reliability.
- Safety Compliance: The SP 3-872-009 meets regulatory standards and represents best practices in safety protocols, reinforcing the importance of maintaining a safe working environment.
- Emergency Response: It serves as a critical control point for electrical distribution, isolating systems during emergencies to reduce fire hazards and other safety risks.
- Proactive Maintenance: The harness offers diagnostic capabilities for ongoing performance monitoring, helping to identify potential issues before they escalate.
- Importance in Energy Sector: The harness is specifically designed for use in power plants, oil refineries, and energy production facilities, ensuring safe operations under high-pressure conditions.
- Overheating Management: To prevent overheating issues in machinery, it is essential to inspect wiring for damage and assess electrical load distribution to avoid excessive power draw on individual components.
Conclusion
The ACTT Service Program’s SP 3-872-009 Shut Down Harness is a vital safety solution in industrial environments. It ensures rapid equipment shutdown during emergencies, significantly reducing risks to personnel and preventing damage to machinery. Built to withstand harsh conditions, it supports proactive maintenance with diagnostic capabilities and meets regulatory standards for safety compliance. Particularly crucial in high-risk industries like energy, chemical processing, and manufacturing, the harness promotes a culture of safety while safeguarding valuable assets. By incorporating this advanced safety tool, organizations can enhance operational safety, protect workers, and ensure regulatory compliance.
FAQs:
1. What is the SP 3-872-009 Shut Down Harness?
The SP 3-872-009 Shut Down Harness is a safety component developed by the ACTT Service Program, designed to enable rapid shutdown of equipment during emergencies, prioritizing operator safety and equipment protection.
2. How does the SP 3-872-009 Shut Down Harness work?
The harness integrates with a machine’s power system and activates upon pressing an emergency stop button or detecting a fault. It promptly disconnects power, preventing further damage and ensuring operator safety.
3. Why is the SP 3-872-009 important in industrial applications?
The harness is crucial in high-risk industries, where operational failures can lead to severe consequences. It ensures immediate shutdown of operations, protecting both workers and valuable assets.
4. What types of conditions can the SP 3-872-009 harness withstand?
The harness is designed to endure extreme conditions, including high temperatures, vibrations, and exposure to corrosive substances, ensuring long-lasting performance in demanding industrial environments.
5. How does the harness support emergency response?
The SP 3-872-009 serves as a critical control point for electrical distribution, allowing for the isolation of systems during emergencies to minimize fire hazards and other risks.
6. Can the harness help with proactive maintenance?
Yes, the harness offers diagnostic capabilities that allow for ongoing performance monitoring, helping to identify potential issues before they escalate into significant problems.
7. In which sectors is the SP 3-872-009 particularly useful?
The harness is specifically designed for use in sectors such as energy production, including power plants and oil refineries, where safe operations are critical under high-pressure conditions.
8. What measures can be taken to prevent overheating in machinery?
To manage overheating risks, it is essential to inspect wiring for damage and assess electrical load distribution to ensure no component is overloaded.
For more Information About Technology visit https://risingperson.com/